化学プラントは大きな設備で製品がどんどんできるところを見るのが魅力的です
自分の携わったものが身近で売られていると仕事に誇りを感じるかと思います
一方で化学プラントも危険なものを扱っているところが多く、常に危険と隣り合わせです
本記事では化学プラントで従事するうえでのきつかった面を敢えて記事にしました
- 化学プラントでの仕事を検討している
- 既に化学プラントで働くことが決まっている
- 化学プラントに従事して経験が浅い
化学プラントでの仕事については以下の記事もご参考に↓↓
化学プラントの仕事できっつかったこと
化学プラントでは危険物が多く扱われいるため、トラブルは常に付きまといます
トラブルといっても種類はたくさんあります
機器・設備関係のトラブル、電気のトラブル、労働災害(一番多いです)、品質トラブルといったトラブルは化学プラントでは日常茶飯事です
どれも納期やお金、ユーザーの信頼に関わるのでどのトラブルであっても対応はきついです
しかし、火災・爆発、漏洩は従業員の命はもちろん近隣住民や環境にも影響を与えるため、対応のレベルが異なってきます
化学プラントでは高圧ガスや危険物、健康に悪影響を与えるものを扱っています
危険が当たり前になり入社当時の敏感さを失っていきます
化学プラントでの重大事故
化学プラントは高圧ガス、可燃性ガス、可燃性液体を多くは使っています
重大事故は、火災・爆発、漏洩(ガス、危険物)です
筆者は火災・爆発、ガス漏洩、危険物漏洩いずれも経験しました
重大事故の中でも爆発とガス漏洩は思い出に残っております
大規模な爆発ではありませんでしたが、それでも音・振動は10m離れた建屋内にも伝わり、初めての感覚で命の危険を感じました
ガス漏洩は目に見えない恐さがあります
当時扱っていたガスが毒性をもつため、吸引すると危険で検知器を頼りにするしかありません
化学プラントは魅力的な一面もありますが、裏では従業員が日々安全に稼働するように努めています
重大事故はいつ起こるかわからない
重大事故にとって休日、早朝、深夜、年末年始とか関係ありません
プラントに危険物がある限り、いつ発災してもおかしくありません
重大事故が発災すると各工場で定められた防災隊が編成され、工場勤務者は召集されます
そして事故が鎮圧するまで、解除されることはありません
プラントはよく生き物と称されます
我々ができることは普段と違うことはないか、違和感を感じることはないか、近くで発災に繋がるような事象はないかにアンテナを張り巡らせるしかありません
ベテランのプラント運転員は感覚が鋭く、いつもと音が違う、温度・圧力が変動する、小説バルブの操作量が違うというように変化に対して敏感です
筆者はベテランの運転員に仕事の相談をしており、危険に対してどこを見るべきか、どこが洩れやすいかを教わっておりました
是非、機械があればベテランの方がいる間に一度は教えて頂きたいものです
重大事故が発災すると辛い
- 早朝・深夜・休日といつ発生するかわからないため、疲れている時は辛いです
- 基本的には屋外で鎮圧まで待機するため、天候が悪い時、夏場、冬場は体に響きます
※長ければ1日続くことも - 事故が鎮圧してからも、製造再開許可に向けて早急に対策を必要があります
休んでいる暇がありません - 事故対応の間にも通常の業務は溜まっているため、業務の処理に追われます
- 発災を知らせるサイレンの音が一気に気分を憂鬱にさせます
- 周囲の人に被害がなければ幸いですが、発災したプラント運転員が心配になります
- 製造再開が遅れると機会損失が増えるため、経営側からのプレッシャーとの板挟みになります
- 安心した途端に事故は再び起こる
発災時の対応は体力的に辛いですが、発災後の対策会議は精神的に辛いです
対策会議が開かれると会議室に箱詰めとなり、なぜなぜが繰り返されます
筆者が爆発を体験した時は、お世話になっていたプラント運転員が発災場所近くにおりました
爆発直前は発災プラントの沿革操作室におりましたが、運転を担当していた人も爆発時にパニックを起こしており、中々正常な対応をとれていなかったことを今でも記憶に残っています
だからこそ、同じことが起きないように事故から我々が今できることを学ぶ必要があります
重大事故から学ぶことは多い
起きてしまった事故はどうしようもありません、後の祭りです
我々にできることは、再び事故が起きないように知恵を絞ることです
実際に事故が起きないと人間は中々動きません
過去に起きているから対策がうたれているからこそ今の安全があります
発災源はどこか、事故前にいつもと違うことはあったか(温度・圧力・原料組成・設備改造・運転条件)、どのタイミングで異変が生じたか、なぜそのような現象が起きたのか、どうしたら異変に気付けるか
事象と運転員が感じた違和感をよく洗い出して、事故原因の掘り下げを行っていきます
事故の原因が絞られ、事故の事象と一致するか確認がとれれば、対策案に頭を使います
生産、機械、電気、プロセスエンジニアが協議して対策を練るため、非常に学ぶことは多いです
対策はハード面とソフト面の観点から協議します
ハード面は設備の追加・改造、安全装置の追加のように物理的な対策を示します
ソフト面は管理範囲の強化や日々の点検、安全シーケンスの構築のようにシステム面・管理面の対策です
安全、品質、コストの順で妥当な対策をその場で決定します
事故が発生すると頭を悩ませることが多くなります
各分野の専門家と協議するため学ぶことが非常に多いです
更に責任が課されるため、これでもかというくらい頭を酷使します
結果、自身の経験となり知見にもなるため成長するわけです
事故を起こさないためにも
事故は人を成長させるわけですが、事故を未然に防ぐに越したことはありません
今いる我々にできることは、過去の事例を学ぶことです
何故起きたのか、どのようなタイミングで起きたのか、どのような考えで対策がとられたか
学べることはたくさんあります
過去の事故事例は以下のプロセス・セーフティー・ビーコン(PSB)から学べますのでご参考に↓↓
過去よりも今の方が技術は進んでおり、装置も計器も進歩しています
今ならこうできるのではないかと考える癖を身につけることが重要です
またプラント運転員と定期的にヒアリングすることも重要です
危険予測の方法は公になっておらず、運転員にしか伝わっていない伝承は意外に多いです
運転員がいち早く気付き、事故に至らない事例は多いんです
しかし上司には詳細が伝わっていないことがほとんどでした
運転員とプラントを廻り、どこに気を付けているか普段からコミュニケーションをとることをお奨めします
環境に慣れてしまうと、危険に対するアンテナが減ってしまう人が残念ながらほとんどです
絶対な安全はありません、危険に対しては臆病なままでいてください
まとめ
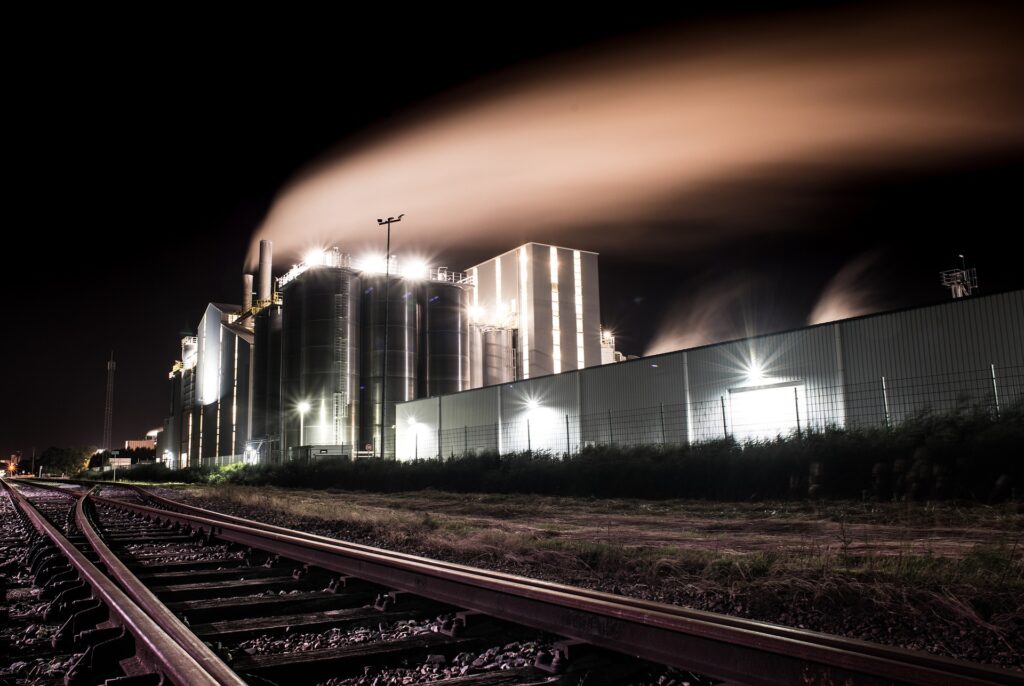
化学プラントは外から見るときれいですが、常に危険と隣り合わせです
事故は発災すると体力・精神ともに想像以上にきついです
きついからといって毎日起こるわけではないので、安心してください
但し、化学プラントもきれいなだけではないということは忘れないでください
そこでは危険と隣り合わせで働いてくれている人がいるということに感謝しています
ご安全に!
コメント